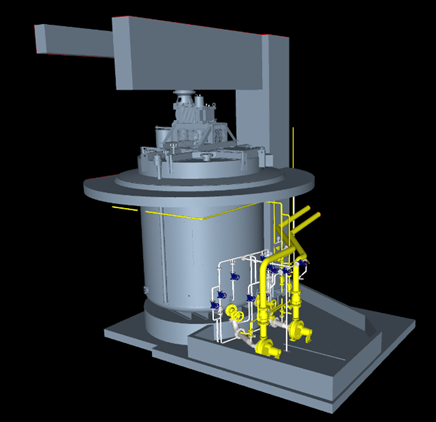
3D modeled tank.
Yara Finland is part of a pure Finnish food chain and has been producing fertilizers in Finland for over 100 years. We have been collaborating with Yara's Kokkola and Siilinjärvi production plants for over ten years, providing mechanical design and laser scanning services, as well as system deliveries in partnership with Rautaseiska Oy. In this article, we will present the benefits of laser scanning in a tank and related piping renewal project.
Taking into account the environment of the equipment and examining the installation arrangements early in the design phase is at least as important for the project's end result as detailed design. Current dimensional data is not always available from production plants, and the objects to be measured are often tight, tall, or have challenging or impossible-to-measure surfaces.
Laser scanning and combining 3D data with scan data is often the only sensible option to ensure that the new equipment fits into the planned location and can be installed considering environmental constraints. Laser scanning also reduces unnecessary factory visits, as the installation site can be visited virtually whenever needed.
In this project, laser scanning was utilized in replacing an old, end-of-life tank with a new tank designed according to the client's specifications. Additionally, some related piping was also replaced. It was clear, right from the beginning of the project, that the tank's environment would be laser scanned to support the tank and installation arrangement planning.
The tank and its surroundings were laser scanned over the course of one afternoon. The point cloud obtained from the laser scanning was cleaned up and transferred to Autodesk Navisworks software. In Navisworks, a 3D model of the tank can be directly placed into the point cloud, virtually positioning it within its actual environment. In addition to the point cloud, the laser scanning data also allows for the examination of precise 360° photos from each scanning point.
Once the 3D model of the tank was placed in its environment, the compatibility of piping modifications and potential collision points or deviations from the original data could be easily verified visually. Utilizing the laser scanning data, piping modifications can be designed with tighter tolerances than usual, thereby reducing material consumption and expediting installation work.
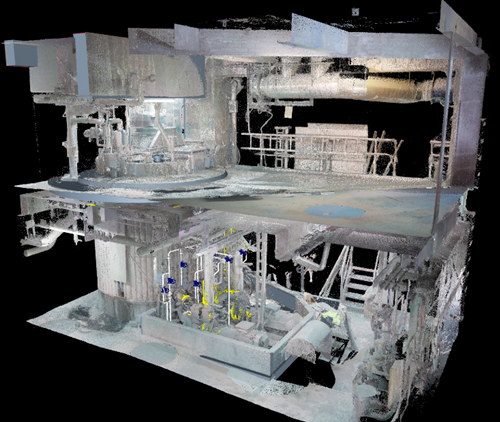
3D model placed in point cloud environment.
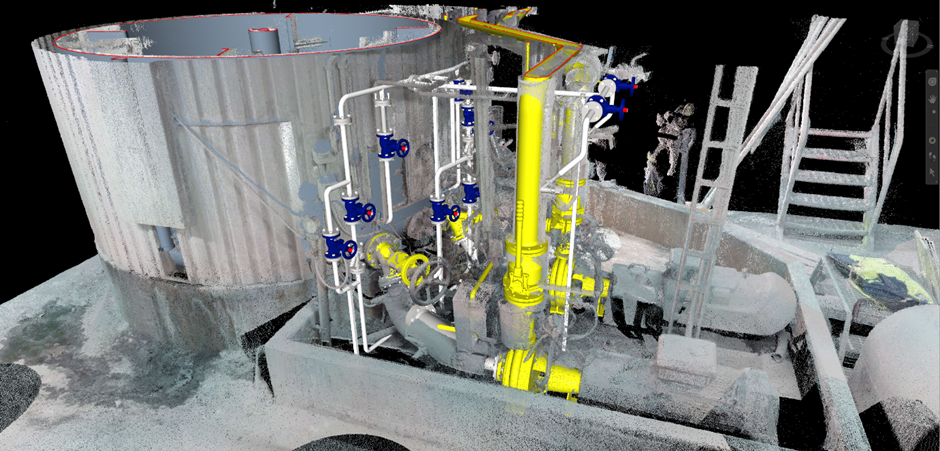
Piping modifications consolidated with the 3D model of the tank.
Since the tank's placement area was tight and divided into two levels, the tank's frame was divided into three main parts for installation, which were prepared in the workshop as much as possible before being transported to the production facility. It is crucial to ensure that the dimensions of the parts allow them to be brought into the production facility considering the constraints of the hauling routes. By utilizing precise measurements from the point cloud data, the heights of the tank's parts were dimensioned to minimize the amount of on-site welding during installation. The hauling of the tank's parts within the production facility was simulated virtually before installation. This ensured that the parts fit into their designated locations along the planned route.
Simo Toropainen, The CEO of Rautaseiska Oy, responsible for the manufacturing and installation of the tank:
Since the 3D design data had already been integrated into the actual environment in advance and installation arrangements could be planned in the early stages, there were no unwanted surprises during installation. The parts fit well into place, and the tank was installed on schedule.
Yara's project manager, Virve Rantakangas, expresses satisfaction with the smooth collaboration and successful outcome:
The project was carried out according to the planned schedule, and the pre-planned lifting and hauling operations went smoothly, and above all, they were executed safely.

Ensuring hauling routes in a point cloud environment.